JTC’s Punggol Digital District (PDD) will be a confluence of technology movers and shakers. But more than just a home, the district will be a living lab. This is made possible by the digital twin component of the Open Digital Platform (ODP). Developed by JTC and GovTech, the ODP’s infrastructure will power up the district.
The digital twin in essence is a repository of data gathered from connected sensors across PDD. Technology developers within the district can harness it to aggressively test their prototypes. Whereas before they would have to pay and settle for lab-generated data, the information in PDD’s digital twin is live, thereby giving them actionable insights as to how their solutions will fare in a real environment.
To prepare for its eventual rollout, JTC’s software engineering team is also testing the digital twin at two other JTC developments: its headquarters, The JTC Summit, and upcoming mixed-use estate Woodlands North Coast. Alan Tan, senior manager and systems team Lead, and Hazel Jung, software engineer, offer us a look at its salient functions, and how it will enable risk-free experimentation as well as streamline operational procedures at PDD.
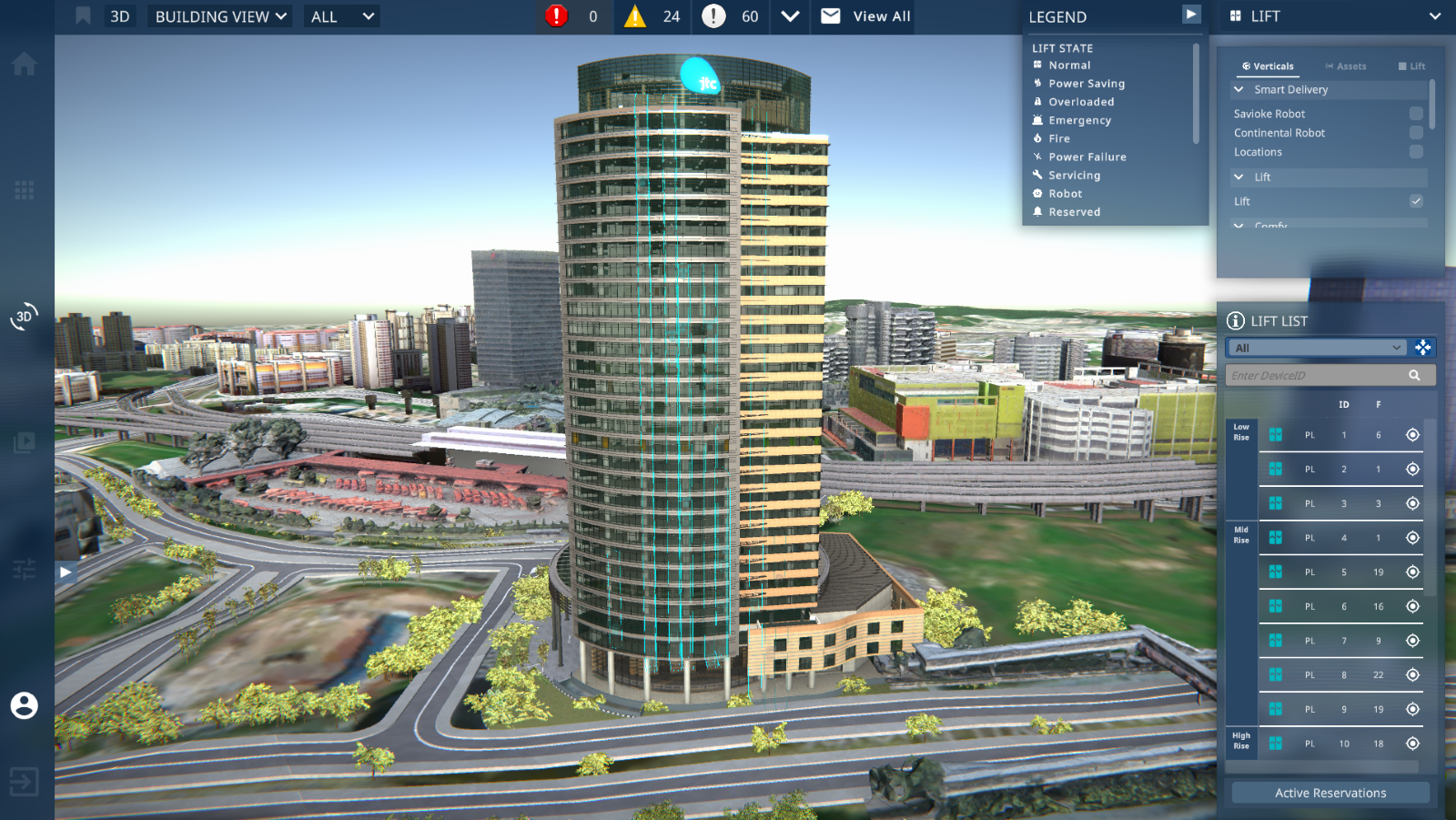
The ODP’s digital twin of The JTC Summit. The digital twin offers a real-time view of developments in a 3D visual format.
First and foremost, what is a digital twin?
Miss Jung: A digital twin is an exact three-dimensional (3D) replica of the physical world. In this virtual environment, the high-fidelity objects represent the array of systems, such as lifts, turnstiles, temperature sensors, CCTV cameras and even mobile solutions such as robots. The digital twin extracts the data layers, and presents them in a way that they become real-time, useful insights for our facility managers.
This is important because from an operations perspective, monitoring is a fundamental yet critical function. All the activities taking place on the ground are reflected on a C3 (command, control and communication) dashboard. Historical data throughout the lifecycle, from status changes to system failures, are also being recorded. The insights help heighten our facility managers’ situational awareness.
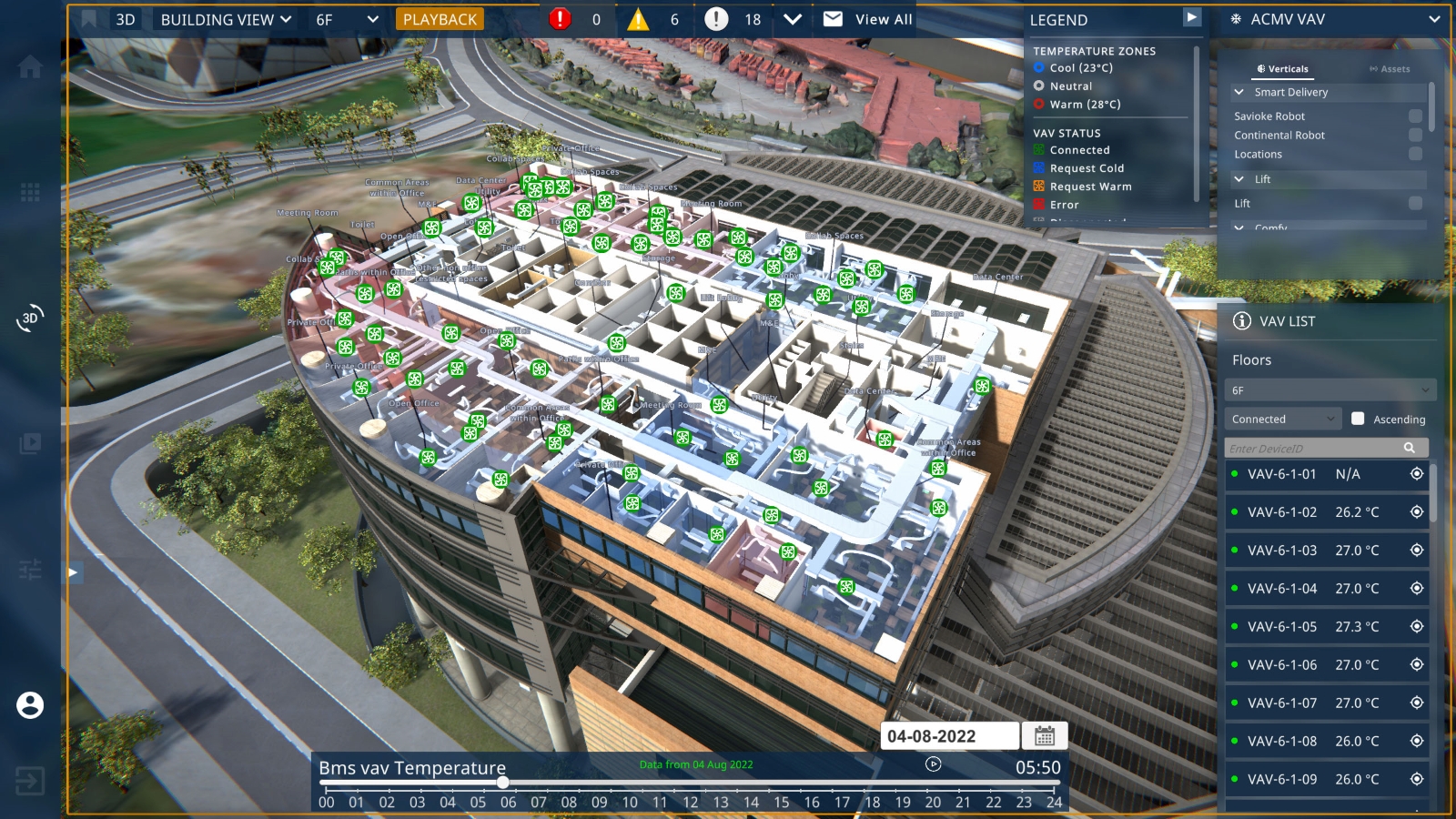
Additionally, the digital twin presents how the 3D objects are related to one another, and their behaviours. What we want to capture ultimately are work processes and field operations. After which, we will be able to optimise our operations more efficiently with artificial intelligence (AI) and machine learning (ML) tools.
What are the solutions used to create this cyber-physical replica?
Miss Jung: There are three main ones: 3D design software, geographic information system (GIS) mapping software and game engine. The 3D design software allows us to virtually replicate PDD. With the GIS mapping software, we can incorporate geospatial data from sources such as the OneMap. Finally, the game engine lets us create scenarios, kind of like missions you have to complete in a role-playing game.
Mr Tan: While the solutions have their unique capabilities, they function in silos. A 3D model is just a model. There isn’t any geospatial data tagged to it, which is critical for a digital twin because we need to be able to pinpoint where our buildings are. So, the ODP gels them together, making the digital twin even more powerful. We now have a 3D model that’s rich with geospatial data, and within this model, we can interact with the objects and run different scenarios.
Could you share a real-world example of how the digital twin will be utilised?
Mr Tan: There are plans to utilise autonomous robots for smart last-mile logistics at PDD, with one aspect being food delivery. When these robots first enter a building, they will make a beeline for the holding area before performing authentication at the gantries. If a gantry is experiencing heavy traffic, the robots will be diverted by the ODP to the next available one. Once they get the greenlight to enter, they will make their way around different levels of the building, during which they will interface with various lift and door systems. For facility managers, knowing if these robots are authorised to enter the buildings is pivotal. They will also need to be able to track their whereabouts. The C3 dashboard allows them to do so, all from a central location.
One of the exciting features of PDD is its ability to be a living lab where companies can test-bed novel solutions without any risks. Could you tell us more about it?
Mr Tan: Robotics developers are already test-bedding their solutions with the living lab. Even though the physical site is still not completed, the cyber-physical replica of PDD already mirrors everything, from lift to door systems, in accordance with the blueprint. Before the advent of PDD’s digital twin, it was rare for them to have such a comprehensively designed virtual world. And they need one when designing applications for their robots, because they have many variables to test. In the food delivery case, they have to first understand how the robots would navigate from the shopping mall to a building. Conducting physical trials to get answers is unfavourable, as it will be very costly.
With PDD’s digital twin, they can deploy simulated robots in a virtual world, let them run wild, and observe their reactions when interfacing with different systems. They can even set conditions, such as wet weather, to see how the robots will navigate their usual routes on a rainy day.
We anticipate that when more developers come onboard and run their data concurrently, we will get to see how different brands of robots can interface with one another, and work hand in hand. That is the synergy the ODP, with its key function of enabling independent systems to interoperate, can achieve.
There are five levels of digital twin, and with each ascension comes new abilities. Could you take us through them?
Miss Jung: The creation of a digital twin begins with the Building Information Modelling (BIM) process. The 3D model generates and manages comprehensive digital information of all the physical assets in PDD. Take for example the pipelines. Details such as the levels they’re installed on are readily available. Next is Level 2, the Informative Twin. Live data, from temperature to weather and power consumption, as well as data from government initiatives such as OneMap, are integrated with the digital twin. It is this marrying of real-time data that enables the function of tracking the robots’ whereabouts.
A digital twin of Woodlands North Coast with tagged physical assets, which can be quickly and effectively located in the digital twin for maintenance and troubleshooting.
Mr Tan: Construction companies can benefit from Level 1 and Level 2. Based on historic data such as rainy season, they can better plan for their projects and make decisions on how quickly they can get their sites up. As for Level 3, or Predictive Twin, we leverage computational fluid dynamics to run simulations. This level gives us the ability to perform predictive maintenance, through the input of historical and real-time data such as human flow and building temperature. For example, we anticipate that in the aftermath of a train fault, crowds will form and take shelter at certain hotspots within PDD. With the simulations, we know where to deploy security personnel so they can perform crowd control. We can also increase the airflows of the air-conditioning units to improve ventilation at these hotspots.
Miss Jung: Level 4, the Comprehensive Twin, is where we model simulations of future scenarios. It is still in its embryonic phase. But the potential of this level is allowing companies to run their simulated data, so that they can create a foolproof contingency plan. The simulations help answer the “what if” questions. For example, what if it rains?
Typically, when planning for scheduling optimisation or downtime, lift vendors do not take into consideration factors such as weather, because lifts are not being deployed in outdoor settings. But we know that inclement weather indirectly affects the scheduling of the lifts. For one, the floors of the lifts will get slippery due to dripping-wet umbrellas, necessitating the activation of a cleaning crew. The temporary shutdown of a lift will affect the wait time; crowds may begin to form at the lobby. With the Comprehensive Twin, our facility managers can input data on weather forecasts, the building’s traffic flow, and lift operations to run tests. After running the simulations, they can identify and close any loopholes in their plans, and know the ideal time when cleaning should take place to minimise disruption, and how quickly it needs to be completed, so that lift services will still run optimally.
Mr Tan: And finally, the pinnacle is also known as the Autonomous Twin. At this level, the ODP, backed by AI and ML modules, will oversee all the decision-making throughout the entire facility management cycle. The system will intuitively know to lower the indoor temperature when a meeting room is fully occupied.
Why is the digital twin, and the ODP, such an important tool in designing a smart business estate?
Mr Tan: We’ve talked at length about how the digital twin consumes real-time data. But in reality, it doesn’t just consume; it is also piping data back to the physical assets. The two highways run parallel. This gives us the ability to perform predictive maintenance. Any potential fault — arising when the different solutions interface with one another — would show up as a reaction in the digital twin. With that knowledge, we can work on preventing the fault from taking place altogether, thereby minimising any time wastage when it comes to the actual rollout.
The digital twin, and by extension, the ODP, bring together different smart solutions and make them smarter. For example, lifts are currently operated by a central controller. They lack the intelligence to optimise their scheduling to serve heavy traffic during peak hours. With AI and ML modules, the ODP will utilise footfall data from CCTV and gantry systems to autonomously send lifts to respective floors. Ultimately, integrating smart operating systems into our infrastructure can help optimise PDD’s resource efficiency and improve user experience.